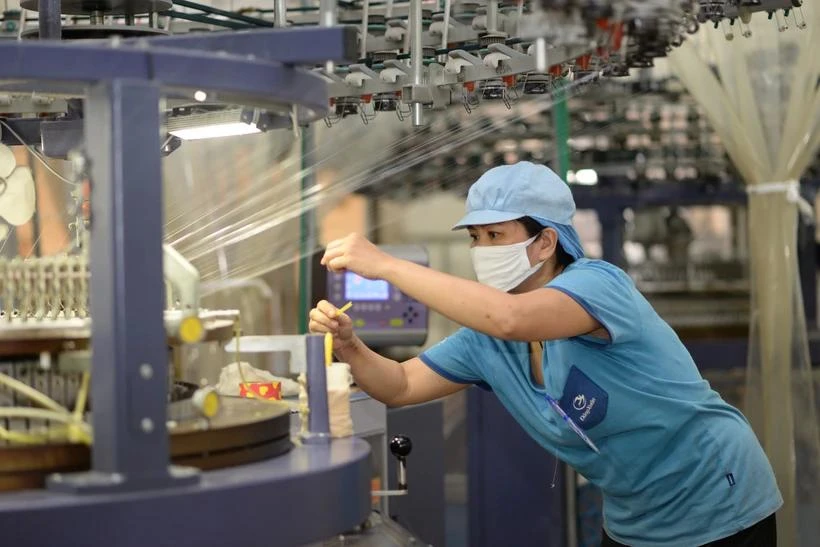
Hanoi (VNA) – Garment and textile enterprises must renew technology, move toward green production and bolster trade promotion, among others, to navigate headwinds, according to insiders.
Although the sector witnessed recovery since the outset of the year, with export revenue during January-April rising 7.5% year-on-year to 12.5 billion USD, challenges remain, including supply chain risks, digitalisation, circular economy and green production, the Vietnam National Textile and Garment Group said.
Vice Chairman of the Vietnam Textile and Apparel Association (VITAS) Truong Van Cam stated that Vietnam gained 44 billion USD from garment and textile export in 2022, which fell to only 39.5 billion USD in the tough year of 2023.
This year, the sector is striving to get back to the 2022 level, he said, adding it will strive toward sustainable development based on digital transformation and green growth by 2030.
Chairman and General Director of Viet Thang Jean Company Limited Pham Van Viet said that to achieve the set goals, enterprises must focus on restructuring and applying advanced technology to improve productivity and product quality, while enhancing multilateral cooperation and boosting the sales of original equipment manufacturer and free on board (OEM/FOB) goods, among others.
He particularly laid stress on the significance of the application of state-of-the-art technology into production and digitalisation, saying fastidious markets like Europe and the US impose strict requirements on green production.
Viet Thang Jean has gone green to better its operation and protect the environment, he said, adding the company invested in a 12.5 million-USD conveyor belt production which does not have negative impacts on the environment.
Besides, automatic fabric cutting machines, nano-dye technology, and Turkish washing technology, among others, have been applied in the company, helping it gain the Oeko-Tex certificate which guarantees Viet Thang products are free from harmful substances, he stressed.
Other firms in the industry have jumped into the bandwagon to switch to modern production models that are friendly with the environment so as to gain advantages while engaging in the global supply chains.
Fadatech fabric dyeing and printing JSC has applied digital printing technology to protect the environment, according to its Director Nguyen Huu Phuc.
He added that costs related to the technology shift are high as the firm has to send its staff abroad for training on new technology.
Viet held that amidst economic challenges, the industry needs more time to seek orders to improve their profits and make technology investment to improve production efficacy./.